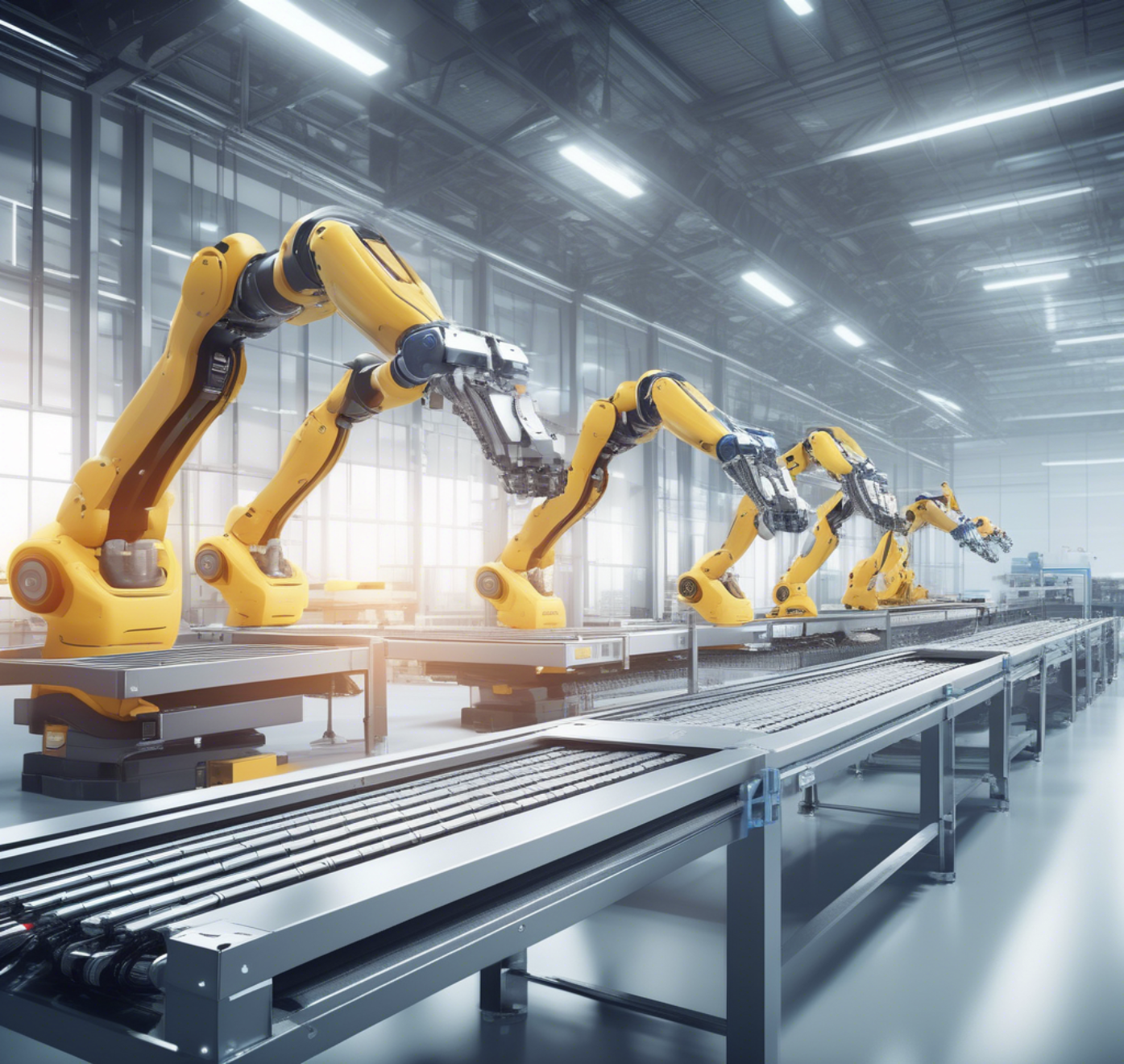
In today’s fast-paced manufacturing environment, industrial robots are playing a critical role in helping industries scale operations, boost productivity, and maintain consistent product quality. These intelligent machines are no longer a futuristic concept — they are an integral part of modern production lines across the globe.
From automotive assembly to food packaging and electronic component manufacturing, industrial robots are reshaping how work gets done.
What Are Industrial Robots?
Industrial robots are programmable mechanical devices designed to automate repetitive or complex tasks in industrial settings. They are equipped with sensors, controllers, and actuators that allow them to operate with speed and precision. Unlike traditional machinery, industrial robots can be reprogrammed and adapted to perform a variety of tasks with minimal downtime
Types of Industrial Robots
There are several types of industrial robots, each suited for specific applications:
Articulated Robots: Resemble a human arm with multiple joints. Ideal for welding, assembly, and material handling.
SCARA Robots: Known for their speed and rigidity, perfect for pick-and-place and high-speed assembly tasks.
Cartesian Robots: Move along linear axes, used in CNC machines and heavy-load applications.
Delta Robots: Extremely fast and precise, commonly used in food and pharmaceutical industries.
Cobots (Collaborative Robots): Designed to safely work alongside humans, ideal for small and medium-sized enterprises.
Applications of Industrial Robots
Industrial robots are incredibly versatile and can be found in various industries, including:
Automotive: For welding, painting, and assembly of vehicle components.
Electronics: In circuit board assembly, micro-soldering, and component handling.
Food & Beverage: For sorting, packaging, and quality control.
Pharmaceuticals: In sterile packaging, laboratory automation, and inspection.
Metal Fabrication: For cutting, grinding, and handling of heavy parts.
Key Benefits of Industrial Robots
The advantages of using industrial robots in manufacturing are extensive:
Increased Productivity: Robots work around the clock without fatigue, dramatically increasing output.
Enhanced Precision: They ensure consistent product quality by minimising human error.
Cost Efficiency: While the upfront investment is significant, robots reduce labour costs and improve ROI over time.
Workplace Safety: Robots take over hazardous tasks, reducing the risk of injuries.
Scalability: Easily integrated into existing systems and scaled as production needs grow.
The Future of Industrial Robots
As technologies like artificial intelligence (AI), machine learning, and the Internet of Things (IoT) continue to evolve, industrial robots are becoming smarter and more connected. Predictive maintenance, real-time analytics, and adaptive automation are transforming them into autonomous systems capable of making intelligent decisions.
With government support, increasing investments, and rapid industrialisation, the future of industrial robots in countries like India is incredibly promising.
Final Thoughts
Industrial robots are no longer just tools — they are strategic assets for any manufacturer aiming to compete in the modern industrial landscape. Whether you're looking to reduce costs, improve efficiency, or future-proof your operations, now is the perfect time to explore robotic automation.
Write a comment ...