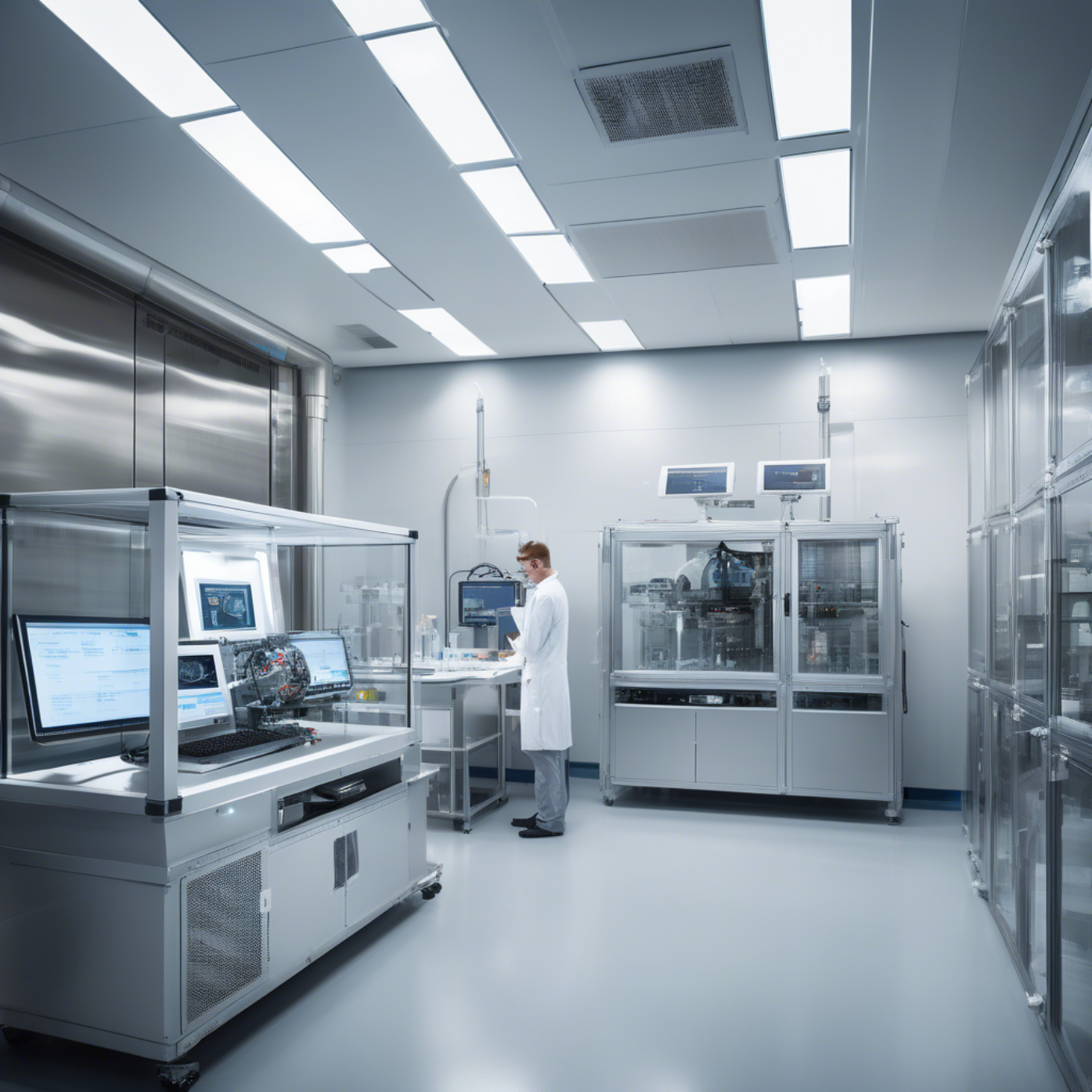
What is an Environmental Test Chamber?
An environmental test chamber is a controlled enclosure used to simulate various environmental conditions such as temperature, humidity, vibration, and altitude. These chambers are crucial in assessing the durability, stability, and performance of materials, components, and finished products before they are launched into the market.
Environmental test chambers help engineers and manufacturers replicate the most extreme real-world conditions in a laboratory setting, ensuring that the products can withstand harsh environments such as scorching deserts, freezing arctic climates, or high-humidity tropical zones.
Functions of an Environmental Test Chamber
Temperature Testing: Measures product performance across a wide range of temperatures, from sub-zero to high heat.
Humidity Testing: Assesses how materials respond to high moisture levels and potential condensation.
Thermal Shock: Evaluates durability against sudden temperature changes.
Altitude Simulation: Mimics high or low-pressure environments, useful for aerospace or high-altitude applications.
Vibration Testing: Simulates vibrations encountered during shipping, operation, or natural conditions.
Corrosion Testing: Assesses resistance to salt spray or other corrosive environments.
Types of Environmental Test Chambers
Temperature and Humidity Chambers: Most commonly used for simulating temperature and moisture combinations.
Thermal Shock Chambers: Have separate hot and cold zones to transfer the product rapidly between extremes.
Altitude Chambers: Simulate high-altitude pressure conditions for aerospace and defence sectors.
Salt Spray Chambers: Specifically designed for corrosion resistance testing.
Vibration Chambers: Combine environmental factors with mechanical stress.
Walk-in Chambers: Large-scale units that allow testing of big equipment or bulk samples.
Applications of Environmental Test Chambers
Automotive Industry: Ensures car components can withstand extreme climates and road conditions.
Aerospace and Defence: Validates the reliability of components in high-altitude and extreme conditions.
Electronics and Semiconductors: Prevents failure of components under fluctuating environmental conditions.
Pharmaceuticals: Test stability and shelf-life of drugs under different climates.
Consumer Goods: Assesses product resilience for everyday use and global shipping environments.
Construction Materials: Evaluates how materials perform over long-term exposure to sun, rain, and temperature.
Benefits of Using Environmental Test Chambers
Product Reliability: Identify weaknesses before the product hits the market.
Regulatory Compliance: Meet industry and government standards (e.g., ISO, ASTM).
Reduced Recalls: Detect potential failures in the R&D phase.
Cost Efficiency: Prevent expensive warranty claims and field failures.
Enhanced Safety: Ensure products remain safe in all expected usage conditions.
Key Considerations When Choosing a Test Chamber
Testing parameters (temperature range, humidity, etc.)
Size and capacity
Type of product being tested
Industry standards and compliance
Budget and maintenance requirements
Conclusion
Environmental test chambers are essential tools in modern product development, ensuring quality, compliance, and performance under real-world conditions. Whether it's for electronics, vehicles, or pharmaceuticals, choosing the right test chamber can significantly impact product success and customer satisfaction. As industries push for greater innovation, the importance of environmental simulation will only continue to grow.
Write a comment ...