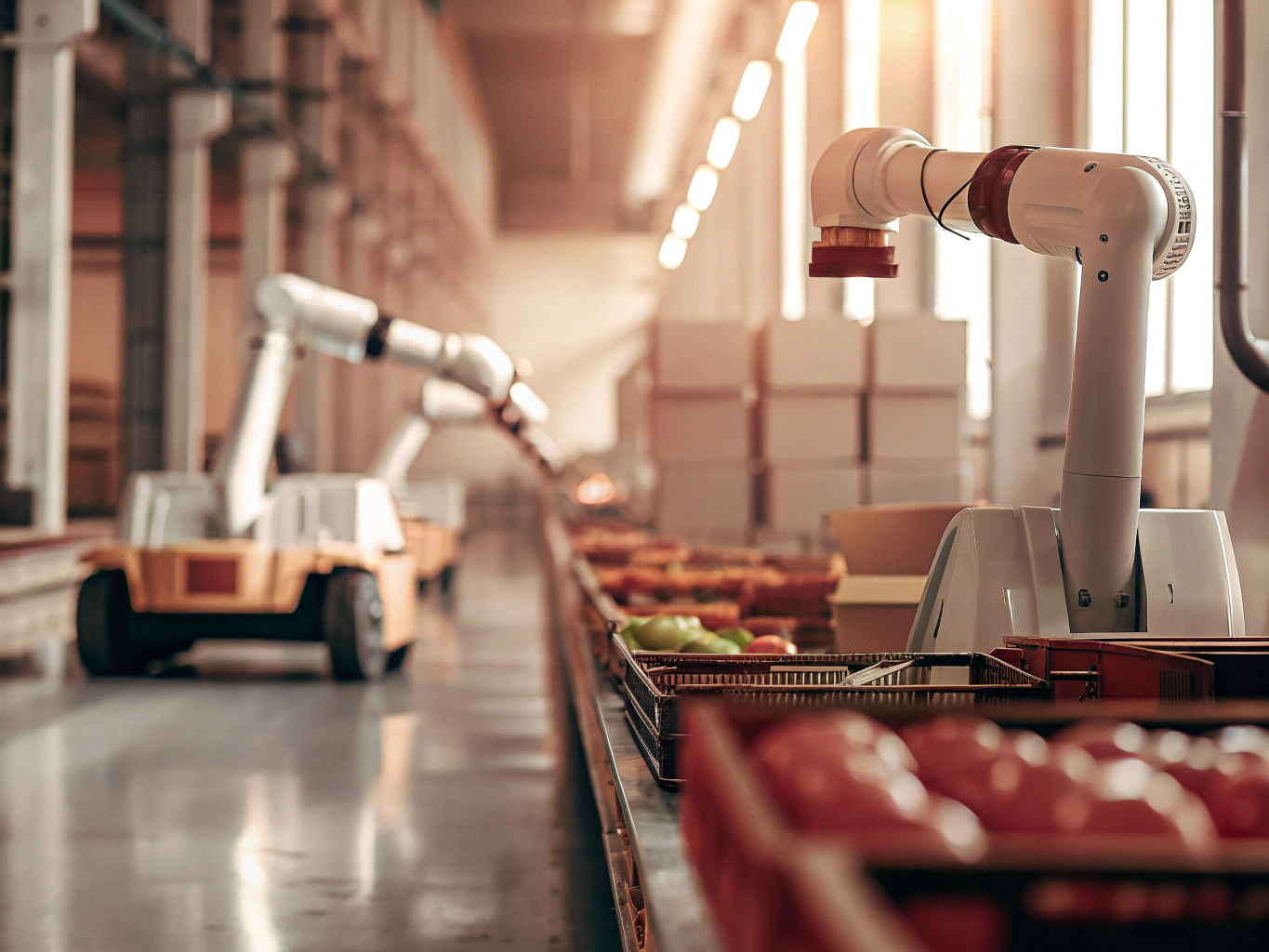
Introduction
The global food robotics market is on fire—projected to grow from USD 3 billion in 2023 to nearly USD 8.9 billion by 2033. From farm to fork, robotics is automating critical processes, improving food safety, slashing labour costs, and accelerating production. Let’s explore how robotics in the food industry is reshaping operations, the benefits it delivers, and how you can implement it in your facility.
What Is Food Robotics?
Food robotics (also called “food industry robotics”) refers to the use of robotic systems in tasks such as ingredient handling, processing, packaging, and even food service. These machines, equipped with arms, sensors, and AI, replace repetitive manual work, maintain strict hygiene standards, and operate around the clock.
Benefits of Robotics in the Food Industry
Enhanced Productivity
Robots work tirelessly at high speeds, boosting throughput by up to 50% compared to manual lines.Consistent Quality & Safety
Automation reduces human contact, cutting contamination risks and ensuring uniform portioning.Labour Cost Savings
While initial investment is significant, ROI often occurs within 12–24 months thanks to reduced staffing needs.Improved Workplace Safety
Robots handle heavy, hot, or hazardous tasks, lowering injury rates and ergonomic issues.Scalability & Flexibility
Programmable robots adapt to new products or line layouts, ideal for seasonal demand spikes.
Key Applications of Food Robotics
According to Proven Robotics, top applications include:
Automated Food Assembly: Building complex snack packs and meal kits.
Ingredient Handling & Dispensing: Precise dosing of liquids, powders, and viscous materials.
Food Sorting & Grading: Using vision systems to separate produce by size, colour, or ripeness.
Coating, Glazing & Baking Automation: Uniform application of batters, sauces, or glazes.
Packaging & Palletising: Case packing, carton forming, pallet stacking at end-of-line.
Quality Inspection: Vision-guided robots detect defects or contamination on conveyors.
Types of Robots in Food Processing
Delta Robots for ultra-high-speed pick-and-place (e.g., confectionery, bakery).
SCARA Robots for lateral assembly tasks (e.g., cup filling, canning).
Cartesian/Gantry Robots for simple XYZ motions—ideal in tight spaces.
Automated Guided Vehicles (AGVs) and AMRs for material transport across warehouses.
Collaborative Robots (Cobots) that work safely alongside humans in packing stations.
Challenges & Solutions
Challenge Solution High Upfront Cost Leverage Robotics-as-a-Service (Raas)Hygiene Compliance Use food-grade materials & CIP systems Integration Complexity Start with pilot lines; modular upgrades Workforce Skills Gap Invest in operator training programs Cybersecurity Risks Implement secure Iot protocols
Future Trends in Food Robotics
AI-Driven Vision & Sorting: Real-time defect detection using deep learning.
No-Code Programming: Intuitive interfaces enabling line workers to reconfigure tasks.
Robotics as a Service (RaaS): Subscription models lowering barriers to entry.
Sustainable Automation: Energy-efficient designs and second-life robot refurbishing.
End-to-End Smart Factories: Full integration with Iot, MES, and cloud analytics.
How to Implement Robotics in Your Food Facility
Assess Your Needs: Map current workflows to identify bottlenecks and manual pain points.
Define Objectives & ROI: Set clear KPIs (throughput, waste reduction, labour savings).
Choose the Right Partner: Look for food-certified integrators with proven case studies.
Pilot & Scale: Start small (single cell), measure performance, then roll out across lines.
Train & Support: Upskill operators and maintenance teams for smooth adoption.
Monitor & Optimise: Leverage data analytics to continuously refine robot performance.
Conclusion
As the food industry tackles labor shortages, stringent safety standards, and rising consumer demands, robotics offers a compelling solution. By automating repetitive tasks—from sorting and handling to packaging and quality inspection—companies achieve faster throughput, better product consistency, and safer workplaces. Investing in food robotics today sets the stage for tomorrow’s agile, sustainable, and high-quality production lines.
Ready to transform your facility with cutting-edge food robotics?
Contact Delta Stark Engineering for a tailored automation roadmap that delivers real results.
Write a comment ...